Penetrant Testing
Add your title here
This is the text area for this paragraph. To change it, simply click and start typing. Once you've added your content, you can customize its design by using different colors, fonts, font sizes and bullets. Just highlight the words you want to design and choose from the various options in the text editing bar.
This is the text area for this paragraph. To change it, simply click and start typing. After adding your content, you can customize it.
Penetrating agents are used to detect discontinuities on the surface of non-magnetic materials. Penetrant testing employs the use of liquid penetrants to make defects easier for an inspector to spot as part of a visual inspection. By applying the liquid penetrants directly to the subject the penetrants with cause any flaws to become more visible. The liquid penetrates into any fissures or voids open to the surface of the test subject. Once the excess penetrant has been cleaned away the remaining penetrant in these areas leaks out.
This can result in flaws that are normally too small to view with the unaided eye to become much more pronounced. Additionally, depending on the size, shape, color, or accessibility of the subject, penetrant testing can allow flaws that may go unnoticed due to their placement in the test subject to be more readily apparent.
- Metals (aluminum, copper, steel, titanium, etc.)
- Glass
- Many ceramic materials
- Rubber
- Plastics
Add your title here
This is the text area for this paragraph. To change it, simply click and start typing. Once you've added your content, you can customize its design by using different colors, fonts, font sizes and bullets. Just highlight the words you want to design and choose from the various options in the text editing bar.
This is the text area for this paragraph. To change it, simply click and start typing. After adding your content, you can customize it.
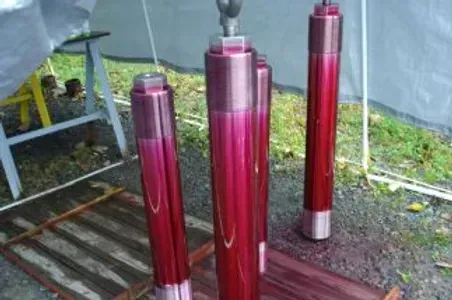
LPI offers flexibility in performing inspections because it can be applied in a large variety of applications ranging from automotive spark plugs to critical aircraft components. Penetrant materials can be applied with a spray can or a cotton swab to inspect for flaws known to occur in a specific area or it can be applied by dipping or spraying to quickly inspect large areas. In the image above, visible dye penetrant is being locally applied to a highly loaded connecting point to check for fatigue cracking.
Penetrant inspection systems have been developed to inspect some very large components.
Liquid penetrant inspection can only be used to inspect for flaws that break the surface of the sample. Some of these flaws are listed below:
- Fatigue cracks
- Quench cracks
- Grinding cracks
- Overload and impact fractures
- Porosity
- Laps
- Seams
- Pin holes in welds
- Lack of fusion or braising along the edge of the bond line
Primary Advantages
- The method has high sensitivity to small surface discontinuities.
- The method has few material limitations, i.e. metallic and nonmetallic, magnetic and nonmagnetic, and conductive and nonconductive materials may be inspected.
- Large areas and large volumes of parts/materials can be inspected rapidly and at low cost.
- Parts with complex geometric shapes are routinely inspected.
- Indications are produced directly on the surface of the part and constitute a visual representation of the flaw.
- Aerosol spray cans make penetrant materials very portable.
- Penetrant materials and associated equipment are relatively inexpensive.
Primary Disadvantages
- Only surface breaking defects can be detected.
- Only materials with a relatively nonporous surface can be inspected.
- Pre cleaning is critical since contaminants can mask defects.
- Metal smearing from machining, grinding, and grit or vapor blasting must be removed prior to LPI.
- The inspector must have direct access to the surface being inspected.
- Surface finish and roughness can affect inspection sensitivity.
- Multiple process operations must be performed and controlled.
- Post cleaning of acceptable parts or materials is required.
- Chemical handling and proper disposal is required.
Entec Consultants offers a full suite of inspection, nondestructive testing, and QA/QC services.
All services offered can be performed in-house or on-site.
Specialized Services
- Video & Fiber optic video boroscope inspection
- AWS-CWI inspectors
- ASNT level III services
- Welder qualifications, Procedure qualifications
- Welder training
- Process safety management & vessel integrity
- Digital cameras
- Autocad & excel reporting
Items Commonly Tested
- Kiln sections
- Structural steel
- Turbines
- Boilers
- Digester vessels
- Pipe welds
- Heat exchanger tubes
- Storage tanks
- Paper machines
- Deaerator tanks