Ultrasonic Testing
Add your title here
This is the text area for this paragraph. To change it, simply click and start typing. Once you've added your content, you can customize its design by using different colors, fonts, font sizes and bullets. Just highlight the words you want to design and choose from the various options in the text editing bar.
This is the text area for this paragraph. To change it, simply click and start typing. After adding your content, you can customize it.
High-frequency sound waves are introduced into a test object to detect and locate internal discontinuities. Ultrasonic testing is a common nondestructive examination (NDE) technique that is designed to use short, high-frequency ultrasonic waves to identify flaws in a test subject. By emitting specific waves into a subject, our team can test the item by measuring the waves after they have passed through the subject. Based on changes to the waves, internal flaws or other properties of the material can be detected.
Our team will use a variety of pulsers, receivers, transducers, and monitors in order to fully test the subject. Based on the results of this nondestructive examination, our team will be able to determine if the subject of the test meets the proper specifications.
Ultrasonic Inspection is a very useful and versatile NDT method. Some of the advantages of ultrasonic inspection that are often cited include:
- It is sensitive to both surface and subsurface discontinuities.
- The depth of penetration for flaw detection or measurement is superior to other NDT methods.
- Only single-sided access is needed when the pulse-echo technique is used.
- It is highly accurate in determining reflector position and estimating size and shape.
- Minimal part preparation is required.
- Electronic equipment provides instantaneous results.
- Detailed images can be produced with automated systems.
- It has other uses, such as thickness measurement, in addition to flaw detection.
As with all NDT methods, ultrasonic inspection also has its limitations, which include:
- Surface must be accessible to transmit ultrasound.
- Skill and training is more extensive than with some other methods.
- It normally requires a coupling medium to promote the transfer of sound energy into the test specimen.
- Materials that are rough, irregular in shape, very small, exceptionally thin or not homogeneous are difficult to inspect.
- Cast iron and other coarse-grained materials are difficult to inspect due to low sound transmission and high signal noise.
- Linear defects oriented parallel to the sound beam may go undetected.
- Reference standards are required for both equipment calibration and the characterization of flaws.
Entec Consultants offers a full suite of inspection, nondestructive testing, and QA/QC services.
All services offered can be performed in-house or on-site.
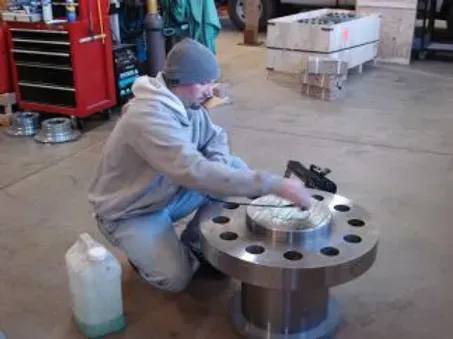
Specialized Services
- Video & Fiber optic video boroscope inspection
- AWS-CWI inspectors
- ASNT level III services
- Welder qualifications, Procedure qualifications
- Welder training
- Process safety management & vessel integrity
- Digital cameras
- Autocad & excel reporting
Items Commonly Tested
- Kiln sections
- Structural steel
- Turbines
- Boilers
- Digester vessels
- Pipe welds
- Heat exchanger tubes
- Storage tanks
- Paper machines
- Deaerator tanks